IKOI Automatic Dosing & Weighing Machine
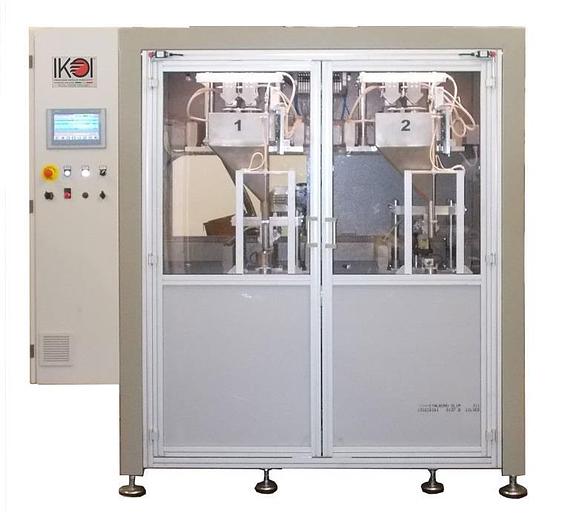
IKOI Automatic Dosing & Weighing Machine
Location:Italy
Description
GENERAL DESCRIPTION OF THE DOSING MACHINE
The machine has been projected in order to automatically weight precious metal grains and dosing it in suitable cups.
The dosing machine is composed of two automatic weighing lines:
-both heads with a maximum productivity of 100/110 weights of 1000 g Au or Ag/hour each.
The dosing plant is composed of the following parts:
- Sturdy painted frame
- Recovery hoppers for the inlet material (grains)
- Lines of pre-weight
- Recovery hoppers for pre-weight
- Lines of final weight
- Finishing cutter
- Cups for the final weight extractable from the plant
- Check electric panel
- Instruction manual
The parts in contact with the precious metal to weight are in stainless steel AISI 304.
Each weighting line can work independently.
The machine is equipped of operator panel where it is possible to memorize the working parameters and up to 20 programs for each weighing line.
The final weight is made on precision loading cells METTLER.
Productivity
- Two heads for weighing from 1 Oz up to 1 kg gold or silver with productivity of 100 pc/h 1.000 g Ag-Au and precision -0,00/+0,02 g
In order to reach the requested weighting precision, the final weight is reaching by adding gold or pure silver calibrated wire.
Description of the Machine:
The dosing machine Z06_200 2T is used to weight gold and silver grains, by obtaining calibrated weights according to the operator setting. The plant is composed of 4 working areas:
1- Grains loading zone
In this zone the operator loads manually on the hoppers the grains to weight. The superior hopper allows to work independently for about 100 weights of 1000 g Au and for about 50 weights for 1000 g Ag.
2- Pre-weighing zone
The loaded grains on the superior hoppers is moved slowly towards 2 vibrating channels for each line which supply the pre-weighing tanks. On the left side, you can see the 2 vibrating channels (a roughing one and a finishing one) of each line; on the right, the grains emptying on the tanks. The grains is weighted and the system prepare a pre-weighing near to the one set from the operator. Once the correct weight is reached, the grain is discharged in a parking hopper. When the pre-weighing tanks are discharged, the system prepare another pre-weight ready for the following cycle.
4-The finishing zone of the weight
From the parking hopper, the grains are moved inside the cups of final weight. In this zone, the weight of the metal discharged from the superior hopper is checked, the quantity of the metal to be added is calculated and the cutter to add the wire necessary to reach the exact final weight is actuated. When the final weighing is finished, the taking door automatically opens and the operator can remove the
cup with the metal inside and place another empty one. The operator is informed from an acoustic signal of the weighing’s end and if the weight is within the tolerance or outside. When the operator places the new cup, the cycle starts again. When the cup is introduced, the system surveys the tare, allowing to work also with more cups.
Description of operator panel
In the operator panel, can be managed all the working parameters of the plant.
- Setting of the pre-weighing weights
- Setting of the speed of the vibrating channels of pre-weighing
- Setting of the weights of the final weighing
- Setting of the cutting parameters of the wire
- Setting of the weighing’s tolerance parameters
- Setting of the material’s discharge times
- Visualization of the plant’s alarms
- Manual management in maintenance function of all the movements of the plant
Instructions Manuals
Complete manual will be provided covering following aspects:
- Complete installation schematics and instructions.
- Operational details.
- Mechanical and electrical schematics, wire diagrams.
- Maintenance manual with parts replacement data and troubleshooting details.
Manual will be in English language
Use and Maintenance Manual.
Every machine is supplied with an English hard copy of:
- Electric, pneumatic scheme;
- Use and maintenance manual.
Security devices according to the Machine Directive 2006/42/CE
The machine with be equipped with an automatic system for the grains’ loading in the superior hoppers. This system allows to load the grains from the ground, in suitable hoppers, avoiding the lifting of the material directly over the machine.
The system is composed of:
- One or two loading hoppers from ground (two hoppers if you desire to work simultaneously with two different metals) in stainless steel, equipped with two wheels for a simple positioning and transfer of the material complete of grains’ suction tube.
- A rapid opening cover is placed on the hoppers basis to allow a fast recovery of the material not used.
- One blower used for generating a depression inside the suction system.
- Electric and pneumatic supply of the blower separated from the dosing plant.
- Two grains receivers placed above the machine properly insulated to avoid the transmission of vibrations to the machine.
- Check system equipped with operator panel to set the working parameters.
Functioning of the automatic loading system:
- The automation is independent from the dosing machine and is foreseen with a separate check system of the material’s level inside the system.
- The grains introduced inside the hopper on the ground is aspirated through a suitable antistatic rubber tube and moved upward above the dosing machine. The suction tube inside the hopper on the ground allow to regulate the grains flow through a simple regulation.
- Above the hoppers of the dosing machine there are the receivers of the grains and, according to the suction times set, they discharge the grains inside the hopper of the dosing machine.
- The receivers are equipped with filter to avoid the grains to reach the blower.
- When the load of the hopper is reached, the grain aspiration is interrupted until a new grains load is requested.
- The suction system is equipped with a suitable paper filter to survey any aspirated metal powders.
- If there are no more grains inside the hoppers on the ground, after same lifting attempts, the suction is interrupted and it reports an alarm.
- With this system, the loaded material is reduced and only the necessary is loaded.
Specifications
Manufacturer | IKOI |
Model | Z06_200 2T |
Year | 2025 |
Condition | New |
Stock Number | 779456 |
Electrical Requirements | 230V / 3 Phase / 60Hz |
Installed power of the dosing machine | 2 Kw |
Treatable Metal | Gold Au 999,9 – Silver Ag 999,9 |
Loading Hopper Capacity | 10 L |
Max loadable gold grain weight | 100 kg for each line |
Max loadable silver grain weight | 50 kg for each line |
Min e max dimensions of the grains | Ø 2-3 mm |
Wire dimensions for the final weighing | Ø 0.5 mm |
Wire loading coil dimensions for the final weighing | DIN125 |
Maximum weight for each cycle | 1.000 g for each line |
Maximum cycle per hour | 100 weighing/h x each line 1000 g Au or Ag, 15 weighing/h x each line 100 Oz Ag |
Compressed Air inlet pressure supply | 6 bar |
Compressed Air flow rate | 270 Nl/h |
Approximative weight | ~1.000 Kg |
Approximative sizes | ~1.000 x 2.200 x h 2.100 mm |
Environment temperature (min-max) | 10 ÷ 35 °C |
Temperature change | Maximum 5°C in 2 hours |
Max relative humidity | min 30% max 70% |